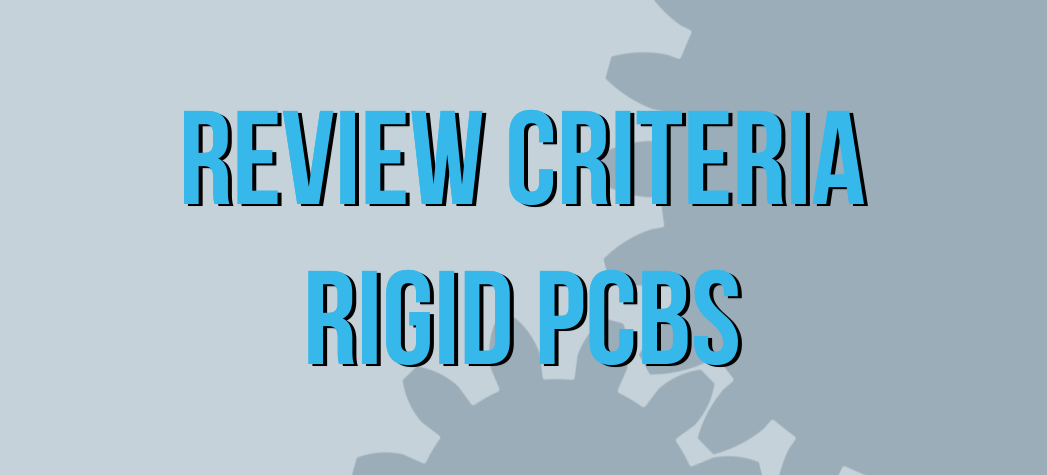
Rigid PCB Review Criteria
It is important to me that I clearly describe for both readers and the manufacturers being reviewed, which criteria are used when evaluating the qualities of both the vendor and the product they provide. These Rigid PCB Review Criteria, in concert with the standardized PCB I designed called a “test coupon” allow me to do a direct technical comparison against a constant design, using the criteria below.
Rigid PCB Review Criteria:
Independence
Manufacturing Reports does not accept compensation of any kind from the manufacturers reviewed, including any discounts or rebates for services provided. For purposes of disclosure, I have dealt with many of the vendors previously, and continue to operate an electrical engineering business that contracts with manufacturers for production runs.
Rigid PCB Review Criteria: Vendor Quality
We evaluate each manufacturer both by evaluating how easy it is to work with them as a business in general, as well as how they deliver as a manufacturing partner. Ease of ordering, variety of services, quality of fulfillment and excellence of customer service are taken into account. We acknowledge that these scores are subjective for the most part.
Ordering Process
How easy was it to order from this manufacturer. Was the ability to upload design files straight forward. Were the ordering options for board stackup and delivery easy to select. How extensive are the ordering options. Are there any unexplained fees. Is an invoice provided at checkout. Are all forms of payment accepted at checkout. Is guest checkout allowed. How clear is the ordering process.
Fulfillment
Was the order shipped on time. What was the quality of the packaging. Are there a variety of shipping options. Was the requested shipping service used. Were there any unexplained shipping fees. Was a tracking number emailed.
Customer Service
Are the accepted design rules easy to find. How easy was it to work with this vendor. Did they respond in a timely fashion when asked a question about the order status. Is the invoice easy to find and download. Do they provide adequate customer support. Is the website easy to navigate, and is the order status page useful. Have they published an email address for customer support. Is a phone number or skype available for customer service. Do they demonstrate follow through. Are they friendly. Do you start receiving spam.
Rigid PCB Review Criteria: Manufacturing Quality
The manufacturing quality of the boards is evaluated both by visual inspection, use of measurement tools and the application of test jigs to determine how close the boards match design files. Tolerances are taken into account where possible.
Each board is ranked by starting at the highest possible score and then subtracting a single point for non-critical issues. The individual board scores are then averaged and any board failure scores are subtracted from the average to determine the overall score for the criteria.
Dimensionality
How closely do mechanical features of the board match the dimensions specified in the uploaded design files. Are the overall dimensions correct and are internal features correctly placed in position relative to others. Are drills the correct size, and slots the correct shape.
Unless otherwise specified by the manufacturer, we use the following tolerances:
- Board Thickness: ±10%
- Overall X Dimension: ±0.2mm
- Overall Y Dimension: ±0.2mm
- Trace Width min. 80%
- Mechanical / NPTH Drills: ±0.08mm
- PTH Drills: ±0.08mm
For via drills we score the possible offset visually as follows. Scores of 3 or 2 are considered non-critical failed drills. A score of 1 is a failed board.
- 5 = Drill on center
- 4 = Drill visibly offset from center
- 3 = Drill offset from center >= diameter of the drill
- 2 = Drill intersects edge of annular ring
- 1 = Drill missed annular ring
Currently our measurement of board outer edge dimensions, NPTH mechanical drills and trace widths has a precision of 0.0005″ (0.5 mil / 0.0127 mm).
For scoring dimensionality, each board starts with a score of 10 and then the following factors are considered:
Item | Score |
---|---|
Board Thickness Exceeds Tolerance | -1 |
Outer Dimensions Exceed Tolerance | -1 |
Non Plated Slots Exceed Tolerance | -1 |
Trace Widths Exceed Tolerance | -1 |
NPTH Dimensions Exceed Tolerance | -1 |
NPTH Jig Failure – Position | -1 |
PTH Jig Failure – Dimension | -1 |
PTH Jig Failure – Position | -1 |
Plated Slots Milled Inconsistently | -1 |
Via Drill Offset Score of 2 or 3 | -1 |
Via Drill Offset Score of 1 | Board Fail |
Unrequested Milled Feature | Board Fail |
Copper Quality
Is the copper weight correct. What is the quality of the surface finish. How easy is it to solder. Are there damaged or missing footprints.
Our tolerance for 1oz copper thickness is minimum 1.4 mil. Surface finish regardless of type is included in that measurement.
Currently our measurement of copper thickness has a precision of 0.0005″ (0.5 mil / 0.0127 mm).
Item | Score |
---|---|
Copper Thickness Below Tolerance | -1 |
Via Damaged (useable) | -1 |
Trace Damaged (useable) | -1 |
Visibly Rough Surface Finish | -1 |
Trace Damaged (unuseable) | Board Fail |
Visibly Damaged Copper Pour | Board Fail |
Footprint Damaged or Missing | Board Fail |
Surface Finish Damaged or Missing | Board Fail |
Solder Mask
Solder mask quality is evaluated visually. How clean is the application of the solder mask. Is there any contamination under the resist layer. Is it well adhered to the copper and of a uniform thickness. Do internal corners appear at risk of tearing. Is the solder mask clearance specified in the design file adhered to.
For scoring the quality of the solder mask, each board starts with a score of 7 and then the following factors are considered:
Item | Score |
---|---|
Mask Offset Onto Pad | -1 |
Mask Size Fails 14mm tolerance | -1 |
Visually Non-Uniform | -1 |
Visibly Thin | -1 |
Visibly Damaged | -1 |
Contaminant Under Mask | -1 |
Easy to remove | -1 |
Exposed Trace or Copper Pour | Board Fail |
Misapplied / Wrong Design | Board Fail |
Silkscreen
Silkscreen quality is evaluated visually. How clean is the resolution of the silkscreen text and artwork. Is it printed on top of exposed copper. Do any graphics or manufacturers markings appear that were not in the design file.
For scoring the quality of the silkscreen, each board starts with a score of 8 and then the following factors are considered:
Item | Score |
---|---|
Low Resolution Direct Legend Printing | -1 |
Layer visibly offset (pads unaffected) | -1 |
No Option to Remove Manufacturers Mark | -1 |
Manuf. Mark Removal Requested but Printed Anyway | -1 |
Unrequested Artwork Printed | -1 |
Reference Designator Illegible | -1 |
Cosmetic Blemishes | -1 |
QR Code Does Not Scan | -1 |
Overprint onto Pad | Board Fail |
Misapplied / Wrong Design | Board Fail |
Solderability
We select one of the manufacturer’s boards at random and examine how it handles having the QFP32 footprint and Micro USB connector soldered to it, and then reworked multiple times. New components are used for each board tested.
The QFP32 is soldered in place using the drag solder method, and then flux is cleaned from the board before the joint is examined. Then the component is lifted with hot air, extra solder is removed from the pads with solder wick, the surface around the footprint is cleaned with 99% Isopropynol and the footprint is examined again. A second round of rework is then performed with the same inspections.
The Micro USB connector is hand soldered to the SMD pads with an iron. The plated slots are not used. After soldering, the board is cleaned with 99% Isopropynol and inspected. The component is subjected to a round of rework using the same procedures as with the QFP32.